North America's first passive house: 'Fire Hall' in Vancouver, Canada
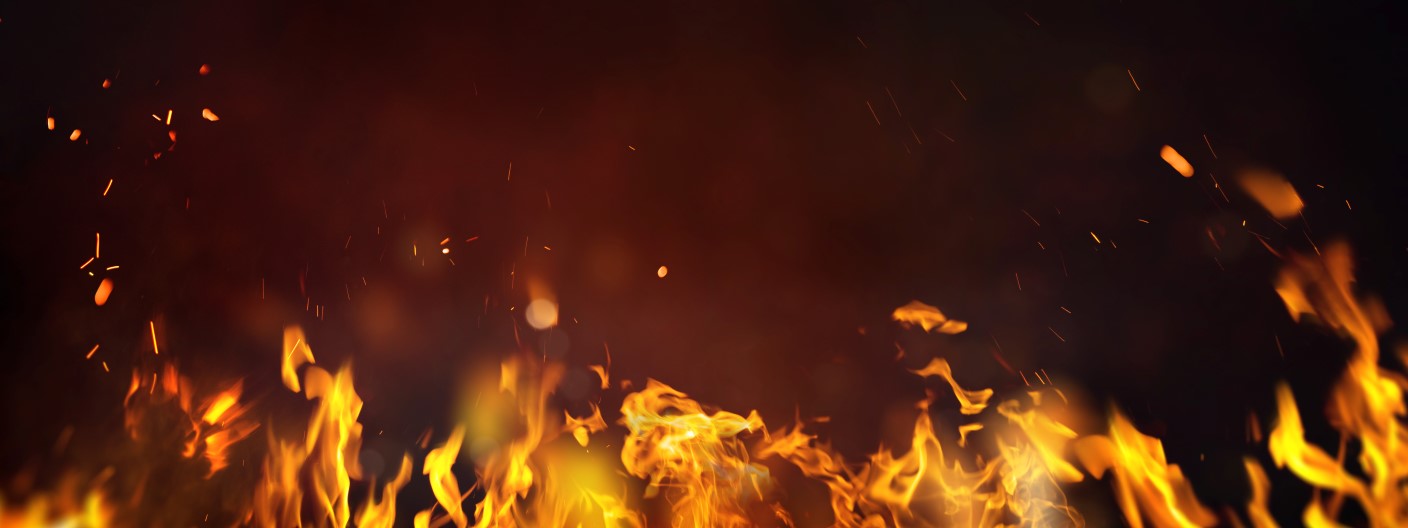
In 2018, the City of Vancouver began the design to replace its fire hall, or also known as a fire station. The new facility is the first fire hall in North America to pursue Passive House certification. The project is also pursuing LEED v4 Gold and Zero Carbon Building Standard certifications. This case study aims to provide an overview of the design and early construction processes and share transferable knowledge.
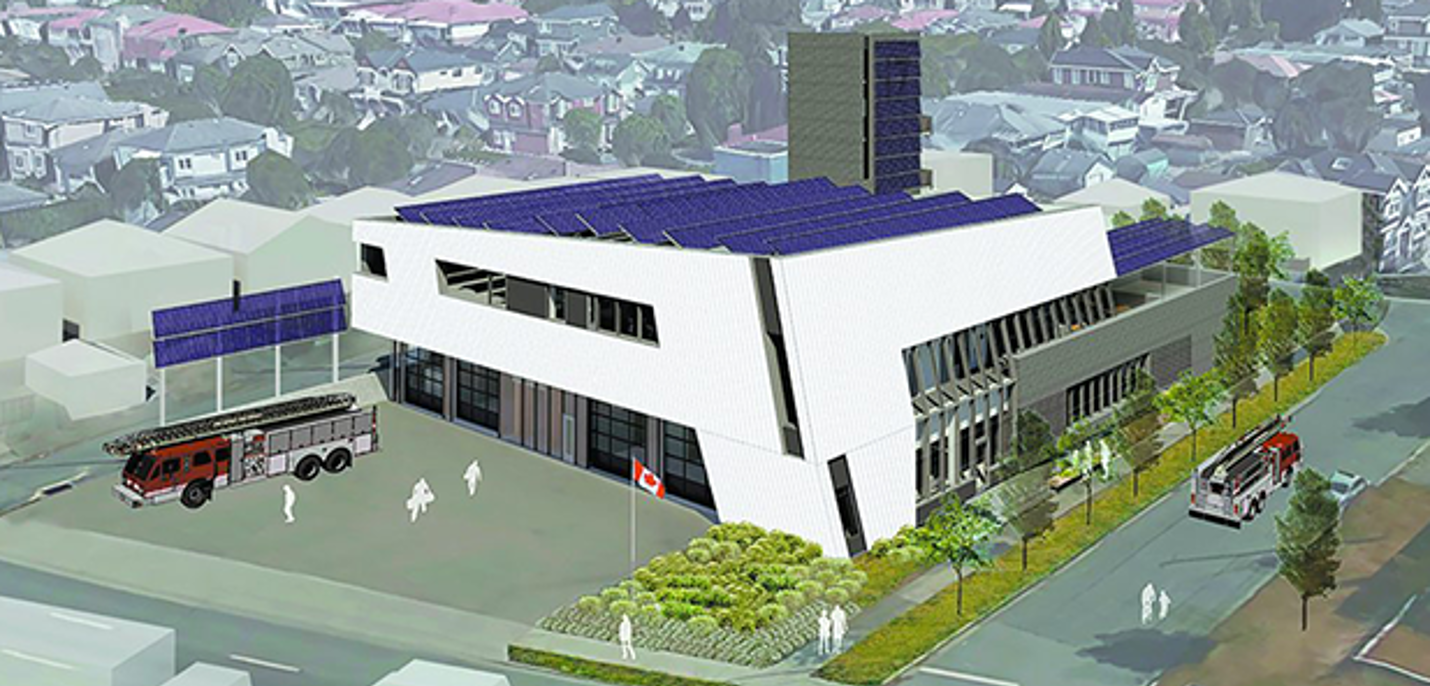
"Vancouver Fire Hall 17 is a response to the urgency of the climate crisis."
— Darryl Condon, Managing Partner at HCMA
Quick facts
Location: Vancouver, Canada
Area: 2,900 m2
Completed: 2021
Architects: HCMA
Certifications: LEED Gold, Passive House, CaGBC Zero Carbon Building and Site Net-Zero Energy
Systems: heat recovery unit (HRVs), radiant heating, heat pump, fan coil, variable air volume (VAV)
Target
Vancouver developed the Zero Emissions Building Plan to address global climate change concerns by developing a roadmap for all new buildings to achieve zero operational GHG emissions by 2030.
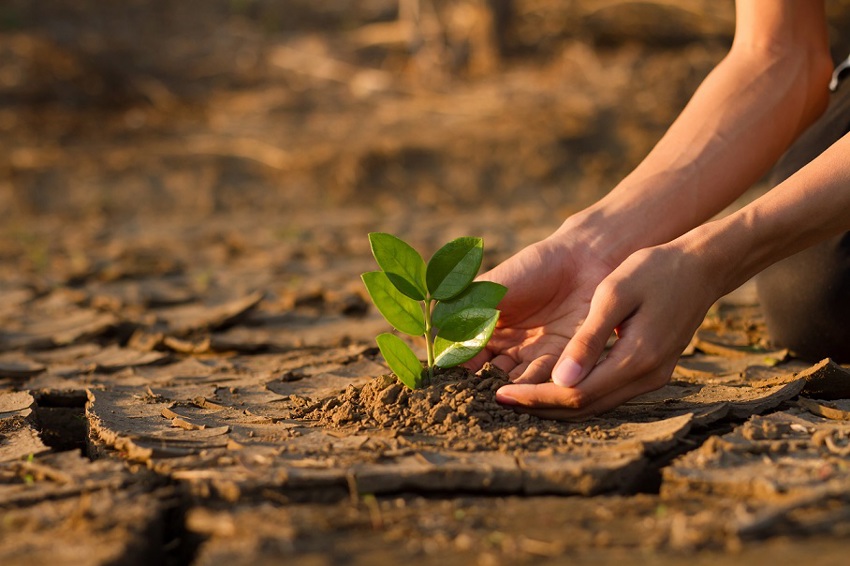
Project context for the future
The City of Vancouver developed the Zero Emissions Building Plan (ZEBP) to address global climate change concerns by developing a roadmap for all new buildings to achieve zero operational GHG emissions by 2030.
Fire Hall No.17 is one of the first city-owned buildings developed under the Zero Emissions Building Plan. The project is serving as a model for other communities looking to increase the energy efficiency of their service buildings.
Fire Hall No.17 in Vancouver
The building type is institutional with a gross floor area of 2,900 m2 and was built in 2021.
The new Fire Hall No.17 is comprised of three main components:
- Apparatus bay with 4 drive-through bays.
- Dual-purpose full-height hose drying and training tower.
- Administration and accommodation spaces, including offices, a training room, a kitchen, a fitness room, and dormitories.
Additionally, the building is equipped with communication and support infrastructure to coordinate all the fire halls in the City of Vancouver in the event of a post-disaster emergency.
To achieve the low carbon and low energy performance targets, design strategies included:
- An optimized orientation to benefit from local climate conditions.
- An airtight envelope.
- Efficient air and water heat recovery systems.
- Low carbon mechanical system that utilizes a geo-exchange field with ground source heat pumps.
The building project team sought to balance the efficiency of the layout design for fire turnout time (the necessary time for crew members to leave the fire hall when signaled) with optimised energy performance. The turnout time requirement and varying building functions resulted in an irregular building shape, which made the design of a high-performance envelope and achievement of the energy-efficiency targets significantly more challenging.
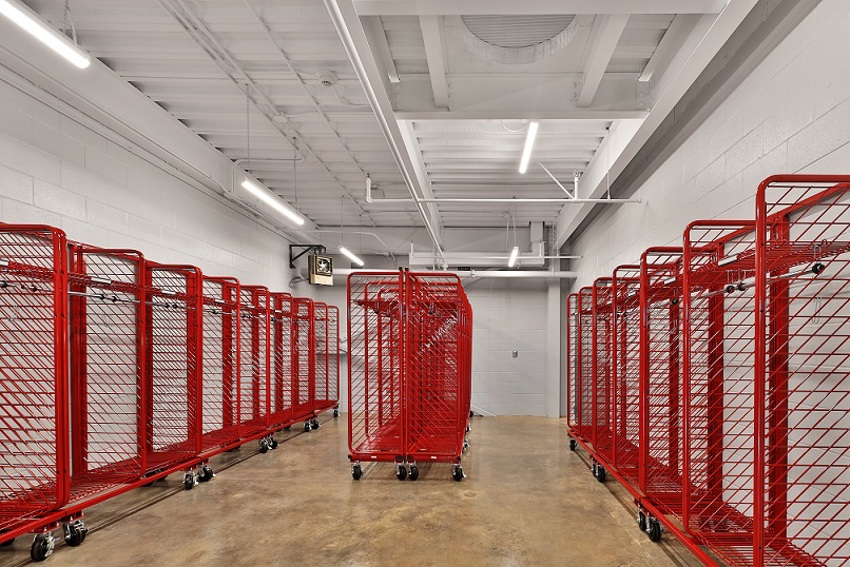
All about zoning
The project team applied an envelope-first design approach to reduce the building's energy loads, before considering improvements to the efficiency of the mechanical systems. The building is split into two envelope zones: the apparatus bays and hose drying/training tower and the administration and accommodation spaces. These zones are independently heated and conditioned to meet different indoor environmental needs and comfort levels.
Each zone is enclosed with a different envelope, designed with levels of insulation based on their interior temperature needs. Both envelope designs are highly-insulated and use Passive House certified windows. Thermal bridges are minimised through the use of thermal breaks and the elimination of mechanical system penetrations.
Also the complex requirements of such a facility led the team to divide the building into two separately certifiable Passive House zones:
- Zone A (living areas) running at 20°C.
- Zone B (four drive-through apparatus bays, a full-size hose/training tower) running at 10°C in winter and 25°C in summer.
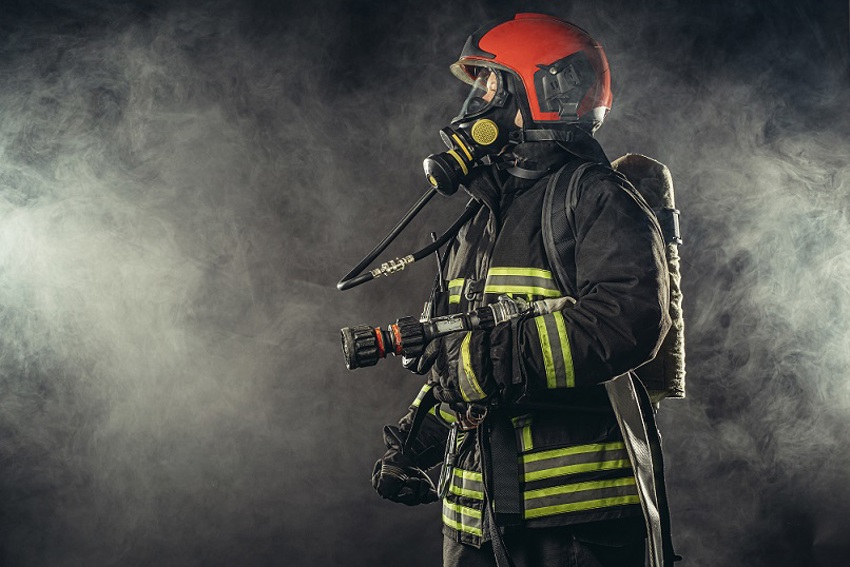
Heating, ventilation and hot water
The heating, ventilation, air conditioning, and domestic hot water systems are fully electric. The building uses a hydronic heating and cooling system with three high-performance ground source heat pumps. Space heating in the apparatus bays is supplied by radiant heating in the concrete floor slabs. The administrative and accommodation areas are heated with fan coil units.
Six heat recovery units (HRVs) are utilised to recover the heat from the exhaust air and heat the incoming air. Using separate HRVs for different zones helps prevent mixing air with different temperatures and reduce the need for reheating air for warmer zones. It also provides better demand control ventilation.
Learn more from the experts
It shows that even large, complex facilities can lead the way in reducing our industry's carbon footprint, while still improving the public service they provide.Darryl Condon, Managing Partner at HCMA
View more case studies
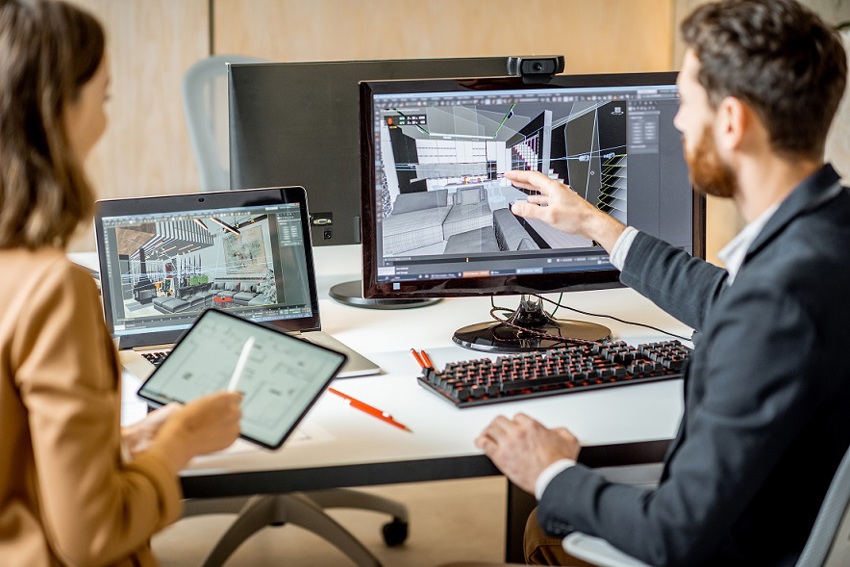
Would you like to know more about building solutions and products?
Passive House certified heat recovery ventilators (HRVs) are an important part of the building system. Using separate HRVs for different zones helps prevent mixing air with different temperatures and reduces the need for reheating air for warmer zones. It also provides better demand control ventilation
Visit Swegon Group to find out more about detailed solutions, components and products for buildings.
Visit Swegon Group to learn more